An innovative technology developed by Aarhus University could revolutionize the recycling of polyurethane, making it more sustainable and recovering up to 82% of the original materials
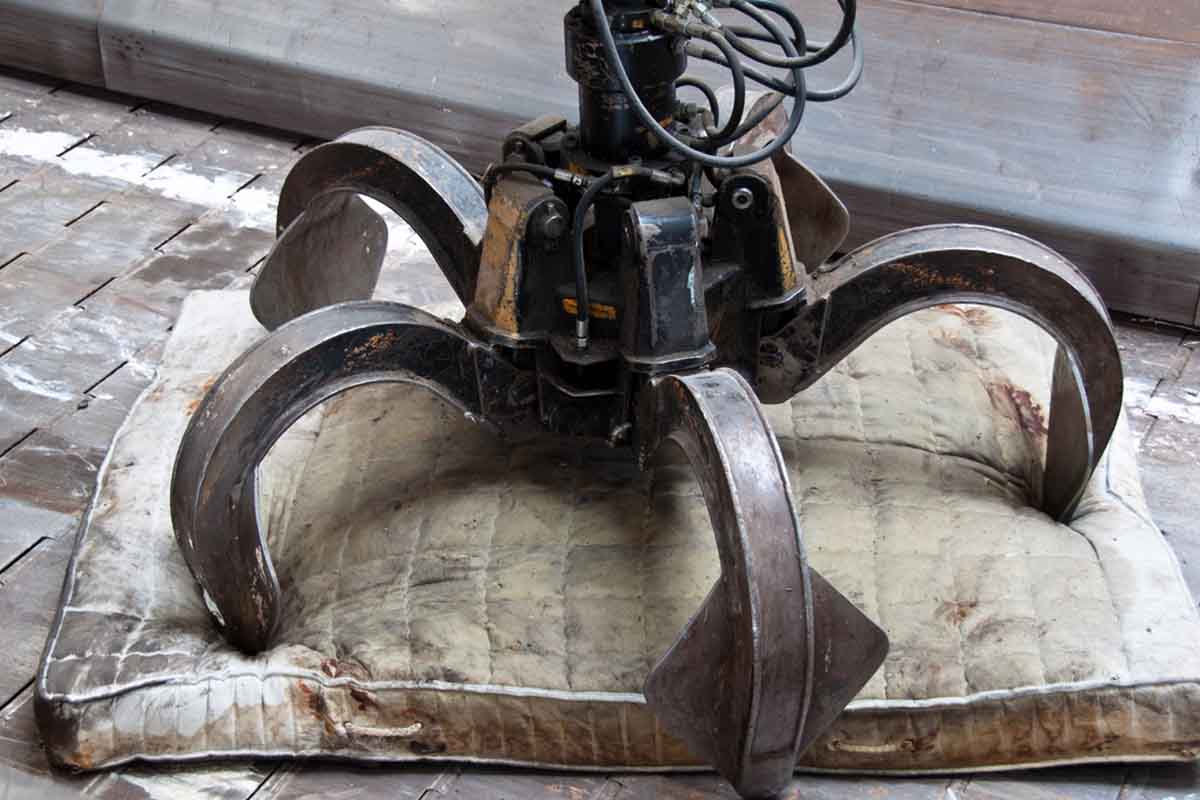
©Aarhus University – Colourbox
PUR is in mattresses, building components, shoe soles, and even in wind turbine rotor blades. While the abundance of applications may qualify PUR as a wonder chemical, its legacy, in respect of environmental impact, should not go unnoticed. Many polyurethane products, at the end of their life cycles, are incinerated or find their way into landfills, an important problem that contributes to environmental issues.
The major raw material used in the manufacture of polyurethane consists of petroleum derivatives, a non-renewable resource. Global production reached a level of 26 million metric tons (28.7 million US tons) in 2022 and will increase beyond 31 million metric tons (34.2 million US tons) by the year 2030, due to demand for foams that comprises 60% of the market.
Polyurethane manufacturing relies on the chemical reaction between polyol and isocyanate, both derived from petroleum. The problem is that such a long molecular chain is hard and very expensive to break down and recycle the material-that is yet to be widespread in industrial-scale practice.
Innovation in depolymerization
Yet not all is lost. One research group at Aarhus University recently developed a new depolymerization technique for polyurethane. The method involves a well-known process called acidolysis, put to work here in a new way: by heating polyurethane foam to 428°F (220°C) along with succinic acid, the team was able to isolate the two major components of polyurethane-polyols and isocyanates-in one step.
The quality of recovered polyols is the same as that of the virgin raw materials, while the residual solid can be transformed into diamines, chemical compounds with two amine groups, -NH₂, in their structure, used for the synthesis of new isocyanates. This process can recover up to 82% of the virgin material and should be regarded as an advanced step towards the recycling of PUR foams.
The road to circularity is thus far from complete. Challenges are not only the expense and complexity of the depolymerization process itself but also in collecting and logistically handling the polyurethane waste. More confusingly, too, each manufacturer makes its PUR with a different formulation, further complicating large-scale recycling efforts.
Researchers continue to experiment with other types of polyurethane and the potential for reusing the acid used in the process. Only time will tell if this can be the starting point for truly sustainable management of polyurethane, but certainly this is a step in the right direction.
Source: Aarhus University